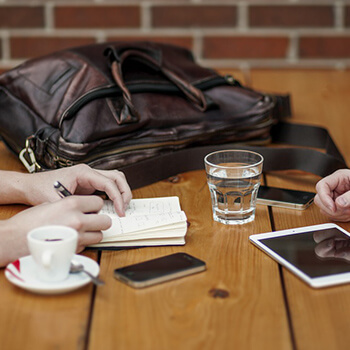
Environmental issues of hybrids
The hybrid vehicle typically achieves greater fuel economy and lower emissions than conventional internal combustion engine vehicles (ICEVs), resulting in fewer emissions being generated. These savings are primarily achieved by three elements of a typical hybrid design:
Relying on both the engine and the electric motors for peak power needs, resulting in a smaller engine size more for average usage rather than peak power usage. A smaller engine can have less internal losses and lower weight.
Having significant battery storage capacity to store and reuse recaptured energy, especially in stop-and-go traffic typical of the city driving cycle.
Recapturing significant amounts of energy during braking that are normally wasted as heat. This regenerative braking reduces vehicle speed by converting some of its kinetic energy into electricity, depending upon the power rating of the motor/generator;
Other techniques that are not necessarily 'hybrid' features, but that are frequently found on hybrid vehicles include:
Using Atkinson cycle engines instead of Otto cycle engines for improved fuel economy.
Shutting down the engine during traffic stops or while coasting or during other idle periods.
Improving aerodynamics; (part of the reason that SUVs get such bad fuel economy is the drag on the car. A box shaped car or truck has to exert more force to move through the air causing more stress on the engine making it work harder). Improving the shape and aerodynamics of a car is a good way to help better the fuel economy and also improve vehicle handling at the same time.
Using low rolling resistance tires (tires were often made to give a quiet, smooth ride, high grip, etc., but efficiency was a lower priority). Tires cause mechanical drag, once again making the engine work harder, consuming more fuel. Hybrid cars may use special tires that are more inflated than regular tires and stiffer or by choice of carcass structure and rubber compound have lower rolling resistance while retaining acceptable grip, and so improving fuel economy whatever the power source.
Powering the a/c, power steering, and other auxiliary pumps electrically as and when needed; this reduces mechanical losses when compared with driving them continuously with traditional engine belts.
These features make a hybrid vehicle particularly efficient for city traffic where there are frequent stops, coasting and idling periods. In addition noise emissions are reduced, particularly at idling and low operating speeds, in comparison to conventional engine vehicles. For continuous high speed highway use these features are much less useful in reducing emissions.
Źródło: https://en.wikipedia.org/wiki/Hybrid_vehicle#Environmental_issues
Surfaces in contact and relative motion
Lubrication
Diagram of an engine using pressurized lubrication
Wikimedia Commons has media related to Internal combustion piston engine lubrication systems.
Surfaces in contact and relative motion to other surfaces require lubrication to reduce wear, noise and increase efficiency by reducing the power wasting in overcoming friction, or to make the mechanism work at all. At the very least, an engine requires lubrication in the following parts:
Between pistons and cylinders
Small bearings
Big end bearings
Main bearings
Valve gear (The following elements may not be present):
Tappets
Rocker arms
Pushrods
Timing chain or gears. Toothed belts do not require lubrication.
Źródło: https://en.wikipedia.org/wiki/Internal_combustion_engine
Mass production of cars
The large-scale, production-line manufacturing of affordable cars was debuted by Ransom Olds in 1901 at his Oldsmobile factory located in Lansing, Michigan and based upon stationary assembly line techniques pioneered by Marc Isambard Brunel at the Portsmouth Block Mills, England, in 1802. The assembly line style of mass production and interchangeable parts had been pioneered in the U.S. by Thomas Blanchard in 1821, at the Springfield Armory in Springfield, Massachusetts.33 This concept was greatly expanded by Henry Ford, beginning in 1913 with the world's first moving assembly line for cars at the Highland Park Ford Plant.
As a result, Ford's cars came off the line in fifteen-minute intervals, much faster than previous methods, increasing productivity eightfold, while using less manpower (from 12.5-man-hours to 1 hour 33 minutes).34 It was so successful, paint became a bottleneck. Only Japan Black would dry fast enough, forcing the company to drop the variety of colors available before 1913, until fast-drying Duco lacquer was developed in 1926. This is the source of Ford's apocryphal remark, "any color as long as it's black".34 In 1914, an assembly line worker could buy a Model T with four months' pay.34
Ford's complex safety procedures?especially assigning each worker to a specific location instead of allowing them to roam about?dramatically reduced the rate of injury. The combination of high wages and high efficiency is called "Fordism," and was copied by most major industries. The efficiency gains from the assembly line also coincided with the economic rise of the United States. The assembly line forced workers to work at a certain pace with very repetitive motions which led to more output per worker while other countries were using less productive methods.
Źródło: https://en.wikipedia.org/wiki/Car#Mass_production